Cutter mill is a type of size reduction equipment, contain blades which reduce material size. Learn its principle working construction uses advantages and disadvantages.
What is Cutter mill in pharmacy?
It also known as a cutting mill. It is a type of size reduction equipment commonly used in pharmaceutical engineering and other industries for the purpose of reducing the particle size of solid materials.
Cutter mill principle
The principle of a cutter mill, also known as a cutting mill, revolves around the reduction of the particle size of solid materials through a cutting or shearing action.
It contains blades, by the help cutter sharp knives material size is reduced.
Construction
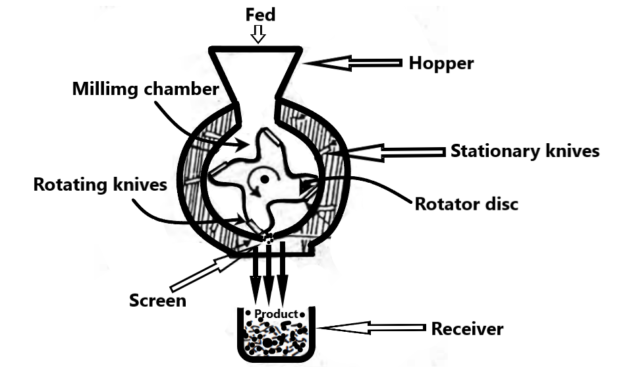
- The disc will rotate in between 200 to 900 revolutions per minute.
- Feed materials will be loaded through the hopper, automatically materials will reach to mill chamber by gravitational force.
- During rotation, materials will introduce with stationary knives and rotating knives.
- Those knives will cut the materials and form smaller fine materials.
- Desired smaller materials will discharge through the screen and collect into a receiver.
Working
The disc will rotate in between 200 to 900 revolutions per minute. Feed materials will be loaded through the hopper, automatically materials will reach to mill chamber by gravitational force.
During rotation, materials will introduce with stationary knives and rotating knives. Those knives will cut the materials and form smaller fine materials.
Desired smaller materials will discharge through the screen and collect into a receiver.
Cutter mill uses
- Cutter mill is used for size reduction of fibrous materials.
- For size reduction of roots, woods of medicinal plants.
- In plastic industry and paper industry this equipment is using for recycling the waste like plastic and paper.
Advantages of Cutter Mills
- Efficient particle size reduction.
- Versatile for various material types.
- Adjustable output size.
- High throughput.
- Effective for wet and dry Materials.
- Sample homogenization.
- Easy cleaning and maintenance.
- Safety features for operator Protection.
Disadvantages
- Potential for heat generation.
- May require multiple passes for fine powders.
- Noise generation.
- Risk of blade dulling.
- Screen clogging with sticky materials.
- Initial equipment cost.
ALSO READ Size reduction definition, methods, mechanism equipment. Size separation objectives applications mechanism in pharmacy.